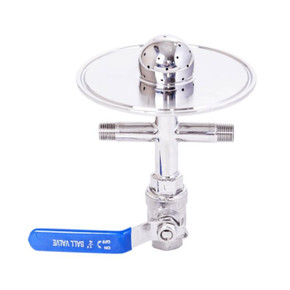
Botanical Health Oils Hardware Ltd
This stainless steel end cap inlet valve is constructed from high-quality 304 stainless steel and comes fitted with an integrated shower head, designed to evenly distribute fluid across the material column—helping to reduce dry spots and improve processing efficiency.
It includes a ¼” female NPT welded ball valve made from 304 stainless steel. Please note that a hose fitting is required to connect tubing to the valve. This can be purchased separately if not already available.
An optional pressure gauge can be added to allow the user to monitor internal pressure within the material column.
This assembly is designed for use alongside a recovery tank. The third port on the unit is multipurpose and is commonly used either to vacuum the material column or to introduce nitrogen into the system from the top of the column.
Enables nitrogen gas integration
Supports vacuum evacuation from the material column
Nitrogen can be a valuable tool in closed-loop systems, as it allows fluid to be transferred efficiently at subzero temperatures without the need for heat input to the recovery tank. The absence of heat promotes better dewaxing performance and contributes to a cleaner end product.
As nitrogen raises system pressure even in cold environments, occasional pressure relief is required. This can typically be done from either the base or the return tank.
Being able to evacuate the system from the column side is highly beneficial, especially when performing multiple back-to-back runs. It allows you to disconnect and reload the column while recovery continues—without dismantling the full system.
When reconnecting the column, the system must be vacuumed again. This cannot be done from the base, which may contain residual oil or liquid. Instead, the hose running back to the recovery tank and the material column itself must be evacuated, all the way down to the ball valve that links to the base.
This is critical for two reasons:
Safety – Air accumulation in the loop can lead to pressure irregularities.
Purity – If air remains in the system, the introduction of dry ice can cause internal condensation, which may affect filtration performance and product quality.
This stainless steel end cap inlet valve is constructed from high-quality 304 stainless steel and comes fitted with an integrated shower head, designed to evenly distribute fluid across the material column—helping to reduce dry spots and improve processing efficiency.
It includes a ¼” female NPT welded ball valve made from 304 stainless steel. Please note that a hose fitting is required to connect tubing to the valve. This can be purchased separately if not already available.
An optional pressure gauge can be added to allow the user to monitor internal pressure within the material column.
This assembly is designed for use alongside a recovery tank. The third port on the unit is multipurpose and is commonly used either to vacuum the material column or to introduce nitrogen into the system from the top of the column.
Enables nitrogen gas integration
Supports vacuum evacuation from the material column
Nitrogen can be a valuable tool in closed-loop systems, as it allows fluid to be transferred efficiently at subzero temperatures without the need for heat input to the recovery tank. The absence of heat promotes better dewaxing performance and contributes to a cleaner end product.
As nitrogen raises system pressure even in cold environments, occasional pressure relief is required. This can typically be done from either the base or the return tank.
Being able to evacuate the system from the column side is highly beneficial, especially when performing multiple back-to-back runs. It allows you to disconnect and reload the column while recovery continues—without dismantling the full system.
When reconnecting the column, the system must be vacuumed again. This cannot be done from the base, which may contain residual oil or liquid. Instead, the hose running back to the recovery tank and the material column itself must be evacuated, all the way down to the ball valve that links to the base.
This is critical for two reasons:
Safety – Air accumulation in the loop can lead to pressure irregularities.
Purity – If air remains in the system, the introduction of dry ice can cause internal condensation, which may affect filtration performance and product quality.