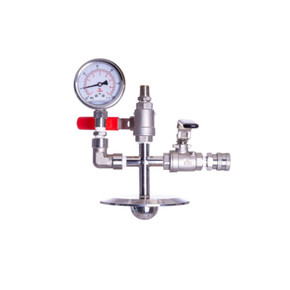
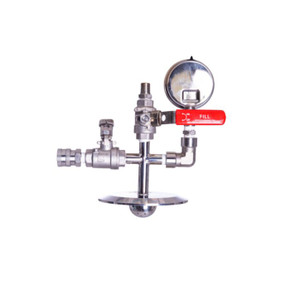
This inlet end cap valve is constructed from 304 stainless steel and comes equipped with a shower head that distributes liquid evenly throughout the material column, helping to reduce dry spots.
The attached pressure gauge is rated up to 100 PSI, with an upgrade option available for 300 PSI.
The unit is supplied with an NPT connection as standard but is also available in JIC, BSP, or socket coupler configurations.
This component is designed to work in conjunction with a recovery tank. The 1/4" male NPT thread at the top is typically used to connect a hose that routes back to the reclamation tank.
It is also possible to attach a 1/4" female NPT hex nut fitting.
The standard configuration includes a 1/4" male NPT thread, enabling the user to directly connect a braided hose to a vacuum pump or a nitrogen cylinder. The upgraded version features a stainless steel socket coupler, offering a quick-connect/disconnect system that simplifies the process and improves efficiency.
Enables the use of nitrogen
Allows for vacuuming the system from the material column
In closed-loop systems, nitrogen can be highly effective. It enables fluid movement at subzero temperatures without the need for applying heat to the reclamation tank. This no-heat approach enhances the dewaxing process and helps achieve a cleaner end product.
As nitrogen increases system pressure even in cold conditions, it may be necessary to bleed the system. This can typically be done from the base or the recovery tank.
Vacuuming from this location is especially useful for users performing multiple cycles. It allows the material column to be disconnected and reloaded while the system is still recovering from a previous run—streamlining operations without dismantling the entire setup.
Once the column is reconnected, the system must be re-evacuated. This cannot be done from the base (as it will contain residual fluid), so vacuuming must take place through the hose leading back to the recovery tank and the material column itself, down to the ball valve at the base.
This step is essential for two key reasons:
Safety – Air accumulation in the loop can pose serious risks under pressure.
Purity – Trapped air may cause internal condensation when dry ice is introduced to the jacket, leading to moisture buildup, compromised filtration, and reduced extract clarity.
This inlet end cap valve is constructed from 304 stainless steel and comes equipped with a shower head that distributes liquid evenly throughout the material column, helping to reduce dry spots.
The attached pressure gauge is rated up to 100 PSI, with an upgrade option available for 300 PSI.
The unit is supplied with an NPT connection as standard but is also available in JIC, BSP, or socket coupler configurations.
This component is designed to work in conjunction with a recovery tank. The 1/4" male NPT thread at the top is typically used to connect a hose that routes back to the reclamation tank.
It is also possible to attach a 1/4" female NPT hex nut fitting.
The standard configuration includes a 1/4" male NPT thread, enabling the user to directly connect a braided hose to a vacuum pump or a nitrogen cylinder. The upgraded version features a stainless steel socket coupler, offering a quick-connect/disconnect system that simplifies the process and improves efficiency.
Enables the use of nitrogen
Allows for vacuuming the system from the material column
In closed-loop systems, nitrogen can be highly effective. It enables fluid movement at subzero temperatures without the need for applying heat to the reclamation tank. This no-heat approach enhances the dewaxing process and helps achieve a cleaner end product.
As nitrogen increases system pressure even in cold conditions, it may be necessary to bleed the system. This can typically be done from the base or the recovery tank.
Vacuuming from this location is especially useful for users performing multiple cycles. It allows the material column to be disconnected and reloaded while the system is still recovering from a previous run—streamlining operations without dismantling the entire setup.
Once the column is reconnected, the system must be re-evacuated. This cannot be done from the base (as it will contain residual fluid), so vacuuming must take place through the hose leading back to the recovery tank and the material column itself, down to the ball valve at the base.
This step is essential for two key reasons:
Safety – Air accumulation in the loop can pose serious risks under pressure.
Purity – Trapped air may cause internal condensation when dry ice is introduced to the jacket, leading to moisture buildup, compromised filtration, and reduced extract clarity.