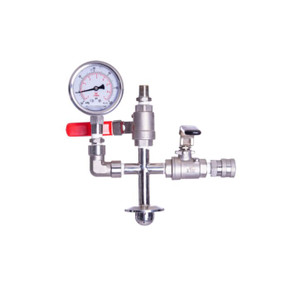
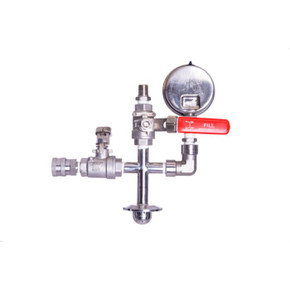
This stainless steel 304 inlet cross end cap valve includes an integrated shower head designed to distribute fluids evenly throughout the material column, significantly reducing the chance of dry spots. It comes equipped with a pressure gauge rated from -30 to 100 PSI, with an optional upgrade to 300 PSI. The unit features a ½” welded female NPT ball valve as standard.
This component is designed for integration with a recovery tank. The 1/2" male NPT thread on the side is typically used to connect a hose returning liquid to the reclamation vessel. It also includes a 1/4" male NPT thread, allowing a braided hose to be hard-plumbed to either a vacuum pump or a nitrogen source. The upgraded configuration offers a stainless steel socket coupler, enabling quick connection and disconnection of the loop for improved operational efficiency.
Enables use of nitrogen assist
Allows vacuum evacuation from the material column
In closed-loop systems, nitrogen plays a valuable role by enabling liquid transfer at subzero temperatures without relying on added heat. This approach supports dewaxing procedures and helps maintain product clarity.
As nitrogen increases internal system pressure at low temperatures, occasional bleeding is necessary to maintain safe pressure levels. This can typically be done from the recovery vessel or the base of the system.
Vacuuming the system from the material column is highly advantageous for continuous or multi-batch processing. It allows you to disconnect and reload the material column while recovery continues — without disassembling the entire system. This saves both time and effort.
After reinserting the column, it’s important to re-evacuate the system — a task that cannot be done from the base, which may contain residual extract. The vacuum must be pulled through the hose connected to the reclamation tank and the column itself, down to the ball valve above the base.
This process is critical for two main reasons:
Safety – Air in the loop can lead to dangerous pressure inconsistencies.
Purity – If air is not fully removed before applying dry ice to the jacket, condensation may form inside the column. This can negatively impact both filtration and final product clarity.
This stainless steel 304 inlet cross end cap valve includes an integrated shower head designed to distribute fluids evenly throughout the material column, significantly reducing the chance of dry spots. It comes equipped with a pressure gauge rated from -30 to 100 PSI, with an optional upgrade to 300 PSI. The unit features a ½” welded female NPT ball valve as standard.
This component is designed for integration with a recovery tank. The 1/2" male NPT thread on the side is typically used to connect a hose returning liquid to the reclamation vessel. It also includes a 1/4" male NPT thread, allowing a braided hose to be hard-plumbed to either a vacuum pump or a nitrogen source. The upgraded configuration offers a stainless steel socket coupler, enabling quick connection and disconnection of the loop for improved operational efficiency.
Enables use of nitrogen assist
Allows vacuum evacuation from the material column
In closed-loop systems, nitrogen plays a valuable role by enabling liquid transfer at subzero temperatures without relying on added heat. This approach supports dewaxing procedures and helps maintain product clarity.
As nitrogen increases internal system pressure at low temperatures, occasional bleeding is necessary to maintain safe pressure levels. This can typically be done from the recovery vessel or the base of the system.
Vacuuming the system from the material column is highly advantageous for continuous or multi-batch processing. It allows you to disconnect and reload the material column while recovery continues — without disassembling the entire system. This saves both time and effort.
After reinserting the column, it’s important to re-evacuate the system — a task that cannot be done from the base, which may contain residual extract. The vacuum must be pulled through the hose connected to the reclamation tank and the column itself, down to the ball valve above the base.
This process is critical for two main reasons:
Safety – Air in the loop can lead to dangerous pressure inconsistencies.
Purity – If air is not fully removed before applying dry ice to the jacket, condensation may form inside the column. This can negatively impact both filtration and final product clarity.