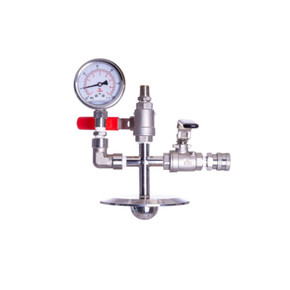
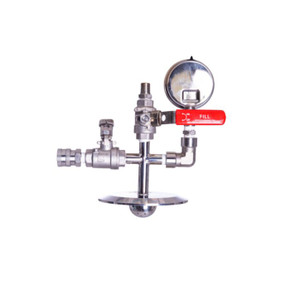
This inlet end cap valve is manufactured from 304 stainless steel and comes complete with a shower head that disperses liquid evenly throughout the material column, helping to prevent dry spots.
The attached pressure gauge is rated to 100 PSI as standard, with an upgrade option available for 300 PSI.
This product is supplied with an NPT connection by default, but it is also available in JIC, BSP, or socket coupler variants.
This component is designed to work in conjunction with a recovery tank. The 1/4" male NPT thread on the top is intended for connecting a hose, which typically routes back to the reclamation tank.
A 1/4" female NPT hex nut fitting can also be attached
Standard configuration includes a 1/4" male NPT thread, which enables direct connection of a braided hose to either a vacuum pump or a nitrogen source. The upgraded version features a stainless steel socket coupler, allowing for quick connection and disconnection, streamlining the entire process.
Compatibility with nitrogen use
Ability to evacuate the system from the material column
In a closed-loop system, nitrogen can be extremely effective. It enables fluid transfer at subzero temperatures without the need to apply heat to the reclamation tank. This absence of heat supports the dewaxing process, yielding a cleaner final extract.
Nitrogen increases internal pressure even at very low temperatures, so it’s important to bleed the system as needed — typically from the base or the reclamation tank.
Vacuuming from this point is essential for running multiple cycles efficiently. It allows the operator to disconnect and reload the material column while recovery continues, without having to dismantle the entire system.
Once reconnected, the system must be evacuated again — a task that cannot be done from the base, which may contain residual fluid. Instead, the hose leading back to the recovery tank and the material column should be vacuumed down to the ball valve above the base.
This is critical for two reasons:
Safety – Air accumulation inside the loop can pose a risk.
Purity – Air trapped in the system can cause condensation when dry ice is applied to the jacket, leading to moisture buildup that negatively affects both filtration and extract quality.
This inlet end cap valve is manufactured from 304 stainless steel and comes complete with a shower head that disperses liquid evenly throughout the material column, helping to prevent dry spots.
The attached pressure gauge is rated to 100 PSI as standard, with an upgrade option available for 300 PSI.
This product is supplied with an NPT connection by default, but it is also available in JIC, BSP, or socket coupler variants.
This component is designed to work in conjunction with a recovery tank. The 1/4" male NPT thread on the top is intended for connecting a hose, which typically routes back to the reclamation tank.
A 1/4" female NPT hex nut fitting can also be attached
Standard configuration includes a 1/4" male NPT thread, which enables direct connection of a braided hose to either a vacuum pump or a nitrogen source. The upgraded version features a stainless steel socket coupler, allowing for quick connection and disconnection, streamlining the entire process.
Compatibility with nitrogen use
Ability to evacuate the system from the material column
In a closed-loop system, nitrogen can be extremely effective. It enables fluid transfer at subzero temperatures without the need to apply heat to the reclamation tank. This absence of heat supports the dewaxing process, yielding a cleaner final extract.
Nitrogen increases internal pressure even at very low temperatures, so it’s important to bleed the system as needed — typically from the base or the reclamation tank.
Vacuuming from this point is essential for running multiple cycles efficiently. It allows the operator to disconnect and reload the material column while recovery continues, without having to dismantle the entire system.
Once reconnected, the system must be evacuated again — a task that cannot be done from the base, which may contain residual fluid. Instead, the hose leading back to the recovery tank and the material column should be vacuumed down to the ball valve above the base.
This is critical for two reasons:
Safety – Air accumulation inside the loop can pose a risk.
Purity – Air trapped in the system can cause condensation when dry ice is applied to the jacket, leading to moisture buildup that negatively affects both filtration and extract quality.