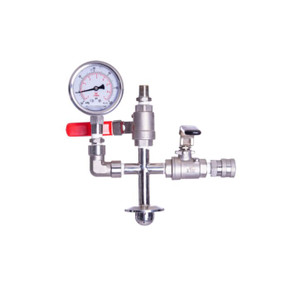
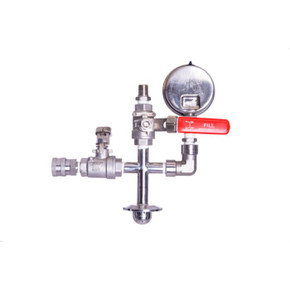
This 4" inlet end cap cross valve is precision-engineered from durable 304 stainless steel and comes equipped with a shower head designed to evenly disperse fluid throughout the material column—significantly reducing dry spots and ensuring consistent saturation.
It features an integrated pressure gauge rated from -30 to 100 PSI, with an optional upgrade to 300 PSI for higher-pressure applications.
Included as standard is a ½” welded female NPT ball valve. The 1/2" male NPT side port is commonly used to connect a return hose routed back to a reclamation or recovery tank.
Additionally, the assembly features a 1/4" male NPT thread, allowing operators to hard-plumb a braided hose to a vacuum pump or a nitrogen source. The upgraded configuration includes a stainless steel socket coupler for fast and secure connections—enabling smoother operation and faster turnaround between runs.
Compatible with nitrogen gas assist systems
Enables vacuum evacuation from the material column
In a closed-loop setup, nitrogen is an effective medium for transferring fluids at subzero temperatures without the need for added heat. Eliminating heat input supports dewaxing and helps produce a cleaner, more refined extract.
However, nitrogen can increase system pressure as it warms, especially at low temperatures. To manage this, periodic bleeding from either the recovery tank or the base is recommended.
Vacuuming from the column side is essential for efficient batch processing. This feature allows operators to disconnect, reload, and continue processing without pausing system recovery—saving time and reducing downtime.
Once the column is reattached, it’s critical to evacuate the loop again. This cannot be performed from the base, which typically contains residual liquid. Instead, vacuum should be drawn through the hose connected to the recovery tank and the material column itself, down to the ball valve positioned above the base.
This ensures two important safeguards:
Safety – Prevents hazardous pressure buildup due to trapped air.
Quality – Removes moisture-causing air that can condense under dry ice, leading to filtration issues and reduced extract purity.
This 4" inlet end cap cross valve is precision-engineered from durable 304 stainless steel and comes equipped with a shower head designed to evenly disperse fluid throughout the material column—significantly reducing dry spots and ensuring consistent saturation.
It features an integrated pressure gauge rated from -30 to 100 PSI, with an optional upgrade to 300 PSI for higher-pressure applications.
Included as standard is a ½” welded female NPT ball valve. The 1/2" male NPT side port is commonly used to connect a return hose routed back to a reclamation or recovery tank.
Additionally, the assembly features a 1/4" male NPT thread, allowing operators to hard-plumb a braided hose to a vacuum pump or a nitrogen source. The upgraded configuration includes a stainless steel socket coupler for fast and secure connections—enabling smoother operation and faster turnaround between runs.
Compatible with nitrogen gas assist systems
Enables vacuum evacuation from the material column
In a closed-loop setup, nitrogen is an effective medium for transferring fluids at subzero temperatures without the need for added heat. Eliminating heat input supports dewaxing and helps produce a cleaner, more refined extract.
However, nitrogen can increase system pressure as it warms, especially at low temperatures. To manage this, periodic bleeding from either the recovery tank or the base is recommended.
Vacuuming from the column side is essential for efficient batch processing. This feature allows operators to disconnect, reload, and continue processing without pausing system recovery—saving time and reducing downtime.
Once the column is reattached, it’s critical to evacuate the loop again. This cannot be performed from the base, which typically contains residual liquid. Instead, vacuum should be drawn through the hose connected to the recovery tank and the material column itself, down to the ball valve positioned above the base.
This ensures two important safeguards:
Safety – Prevents hazardous pressure buildup due to trapped air.
Quality – Removes moisture-causing air that can condense under dry ice, leading to filtration issues and reduced extract purity.