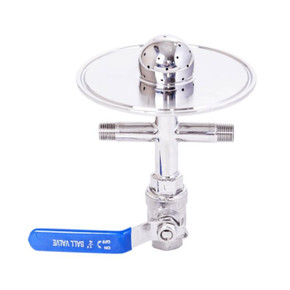
Botanical Health Oils Hardware Ltd
This inlet end cap valve is manufactured from high-grade 304 stainless steel and features an integrated shower head that ensures even fluid distribution across the material column—minimising dry spots and improving efficiency.
It comes standard with a ¼” female NPT welded ball valve, also made from 304 stainless steel. Please note: to connect a hose, a compatible fitting is required. If not already available, this fitting can be purchased separately.
An optional pressure gauge can be installed, allowing users to monitor the pressure within the material column during operation.
This inlet is designed to work in conjunction with a recovery tank. Its third port is multi-functional—commonly used either for vacuum evacuation of the material column or for introducing nitrogen directly into the system.
Allows the use of nitrogen assist
Enables vacuuming from the material column
In closed-loop processing systems, nitrogen provides excellent utility by enabling fluid movement at subzero temperatures—without requiring heat input to the recovery tank. This lack of heat supports dewaxing and promotes a cleaner, clearer extract.
However, nitrogen can increase system pressure at low temperatures, so it’s important to periodically bleed the system. This can be done from either the recovery tank or the base.
Vacuum evacuation from the column side is a major efficiency boost for users running multiple batches. It allows you to disconnect and reload the column while the system continues to recover—no need to disassemble the rig.
When reconnecting the column, you’ll need to evacuate the system again. This cannot be done from the base, as it will typically contain residual oil or other liquids. Instead, the vacuum must be pulled through the hose connected to the recovery tank and through the material column, down to the ball valve at the base.
This process is critical for two main reasons:
Safety – Air left in the loop can create pressure instability or hazards.
Product Integrity – Air in the system may condense when dry ice is applied, leading to moisture buildup in the material column that can compromise both filtration performance and final product quality.
This inlet end cap valve is manufactured from high-grade 304 stainless steel and features an integrated shower head that ensures even fluid distribution across the material column—minimising dry spots and improving efficiency.
It comes standard with a ¼” female NPT welded ball valve, also made from 304 stainless steel. Please note: to connect a hose, a compatible fitting is required. If not already available, this fitting can be purchased separately.
An optional pressure gauge can be installed, allowing users to monitor the pressure within the material column during operation.
This inlet is designed to work in conjunction with a recovery tank. Its third port is multi-functional—commonly used either for vacuum evacuation of the material column or for introducing nitrogen directly into the system.
Allows the use of nitrogen assist
Enables vacuuming from the material column
In closed-loop processing systems, nitrogen provides excellent utility by enabling fluid movement at subzero temperatures—without requiring heat input to the recovery tank. This lack of heat supports dewaxing and promotes a cleaner, clearer extract.
However, nitrogen can increase system pressure at low temperatures, so it’s important to periodically bleed the system. This can be done from either the recovery tank or the base.
Vacuum evacuation from the column side is a major efficiency boost for users running multiple batches. It allows you to disconnect and reload the column while the system continues to recover—no need to disassemble the rig.
When reconnecting the column, you’ll need to evacuate the system again. This cannot be done from the base, as it will typically contain residual oil or other liquids. Instead, the vacuum must be pulled through the hose connected to the recovery tank and through the material column, down to the ball valve at the base.
This process is critical for two main reasons:
Safety – Air left in the loop can create pressure instability or hazards.
Product Integrity – Air in the system may condense when dry ice is applied, leading to moisture buildup in the material column that can compromise both filtration performance and final product quality.